Resources
Advanced Rejection for Food Products Using Vision Inspection
Customized rejection systems designed to customer specifications will remove individual product from the production line once a fault has been detected.
A calibrated vision inspection system, when installed on a commercial bakery or processed foods production line, can remove the operator/inspector cull subjectivity to ensure 100% of products are graded equally. Additionally, the vision system tallies the rejects by fault type, something that is impossible for a manual inspector to perform, allowing data reports to aid staff in making process improvements. Using a variety of methods, non-conforming products can be automatically removed at very high speeds (over 100 objects per second). Manual inspection is prone to uneven results between different employees and may cause collateral waste. Also, a human may only be able to inspect a small number of products on a high-speed and/or wide production line.
Vision inspection systems have several advantages which include:
- Systems are calibrated to ensure measurements are accurate and repeatable, including color in L*a*b and BCU, producing reliable results which allow operators to control rejection criteria in both real-time and through historical analysis.
- High speed rejection methods are easily integrated into the current or new production line which remove 100% of customer designated faulty objects without disturbing the flow of product. Operators can be sure that product going to packing meets specifications.
- Rejection settings are completely in control of production and quality management, producing lower reject rates and reduced wastage.
Accurate, Repeatable Information - Increased Quality - Better Control
Choosing Your Rejection Mechanism
Montrose Technologies works closely with food production clients to choose the most effective and robust rejection solution for their products. The reject module design is influenced by a number of important factors which include – size/shape/firmness/weight of the objects being inspected, the rate of the production line and product presentation (single file, set lanes, random locations across the belt, orientation). Additionally, the reject design is influenced by handling requirements which may include multi-stage sorting or the reuse of faulty product.
Defining the Reject Module by Product Characteristics
Physical characteristics of your food product will define what method of rejection is used. Montrose has a long history of designing and manufacturing rejection solutions for a wide variety of baked and processed food products. Montrose process engineers will work with samples in our application laboratory to find the most efficient rejection solution for each customers specification.
Each Montrose turnkey inspection system is designed to fit production requirements, environments and line layouts as specified by our customer. A rejection module may also be used for further downstream grading and sorting with a mechanical diverter or a second array of air jets.
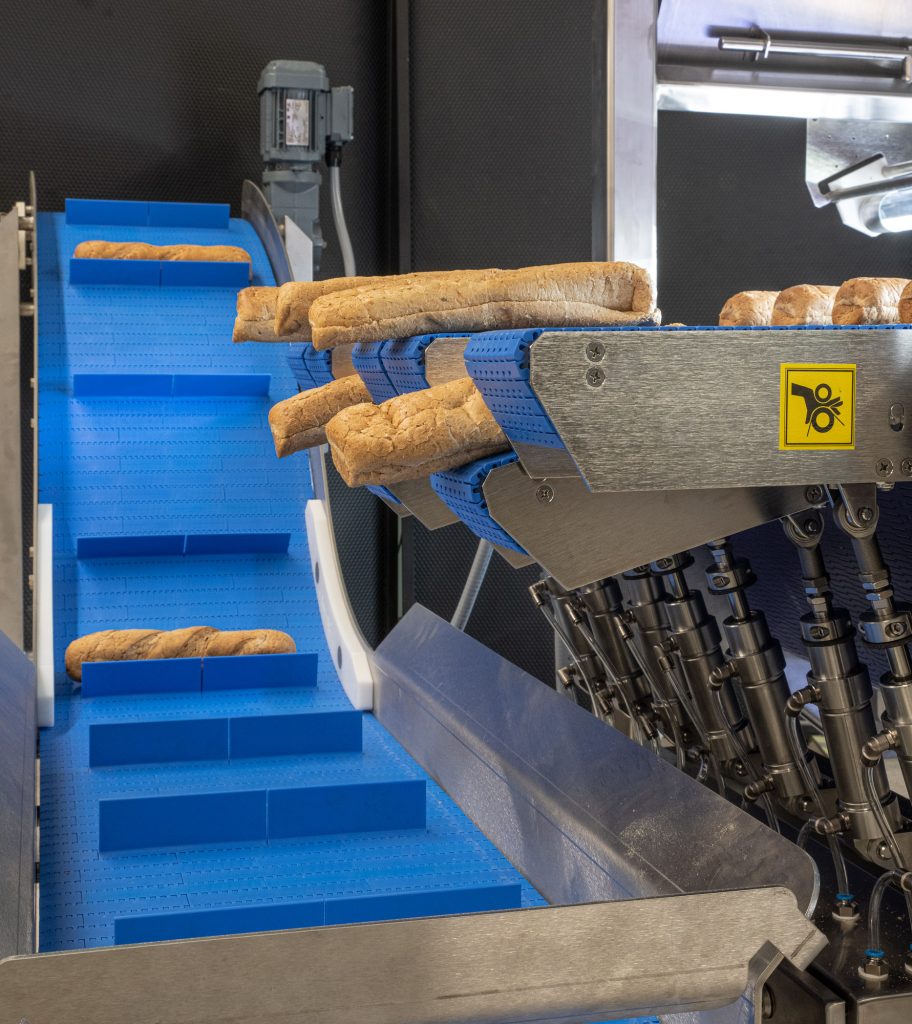
Types of Rejection Modules
Air Jets
An air jet module is the simplest and most widely used rejection method. At Montrose we utilize different types of air jet nozzles which produce various cone shapes of air suitable for specific products. Also product specific is the air pressure, timing and length of air burst which are controlled by MT inspection software. Once a product has been identified by the inspection system to not meet your predetermined quality specification, an air blast will redirect the fault item away from the regular flow of product. This method of rejection works with single-lane or randomly placed product with no disruption in flow.
Horizontal
Horizonal air jet(s) can blow off a product presented in single file or a pair of side-by-side lanes. Examples where this form of rejection may apply include: english muffins and cookies.
Vertical Upwards
An array of downward vertical jets can be used to redirect faulty product down through a gap that good product will span across. For wide variety of products such as tortillas, buns, bagels, rice cakes, toaster pastries and english muffins, air jet rejection is an efficient and reliable rejection method.
Vertical Downwards
For small, slowly moving, light and/or fragile product faulty individual pieces can be redirected with an array of upward jets.
Tipdown Rejection
When products are longer and/or taller, a laned belt-driven tipdown exit can be an effective rejection method. This method is well suited for bread loaves, baguettes, clusters and similar products. Tipdown rejection is suitable for high speed and can be customized to any number of lanes across the belt.
This type of rejection can also be used to separate product into multiple lines and are custom designed for the application complete with automated control software, safety guarding and functionality.
Pusher Rejection
Another kind of rejection method involves a mechanical paddle to physically push the product off the side of the belt. This method is used on larger/heavier single file or dual lane lines such as bread loaves and packaged goods. Push rejection uses a linear actuator to push products off the conveyor into a reject bin.
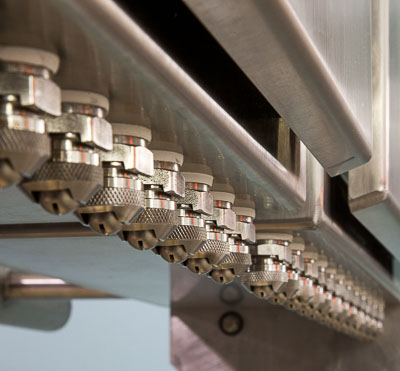
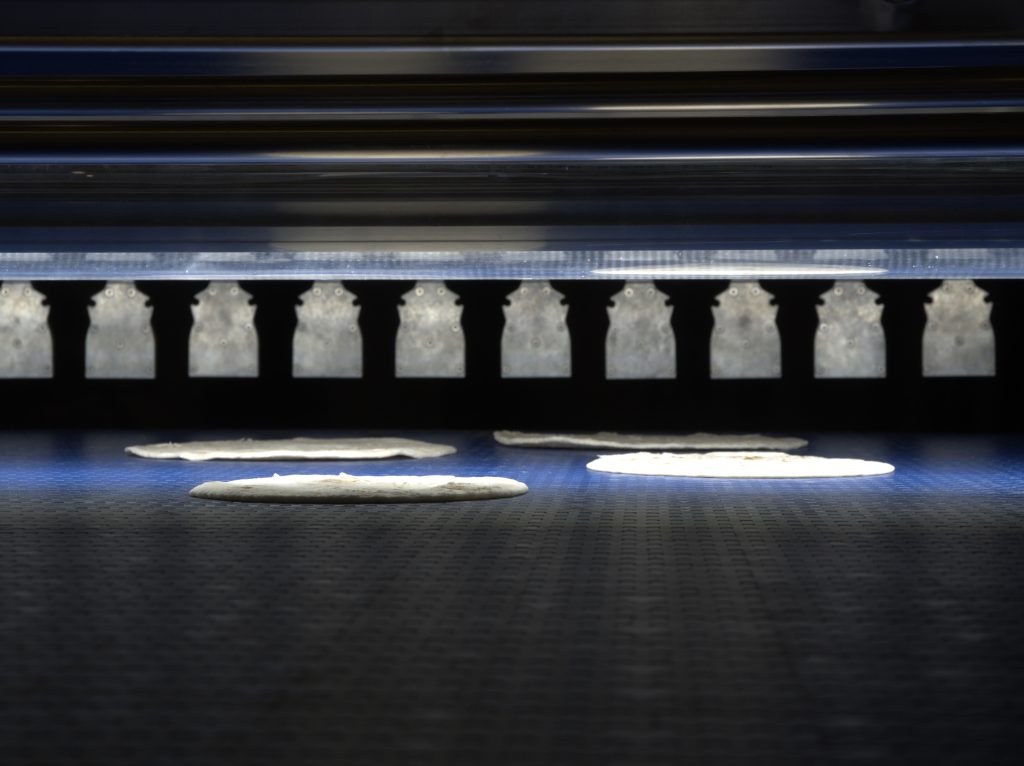
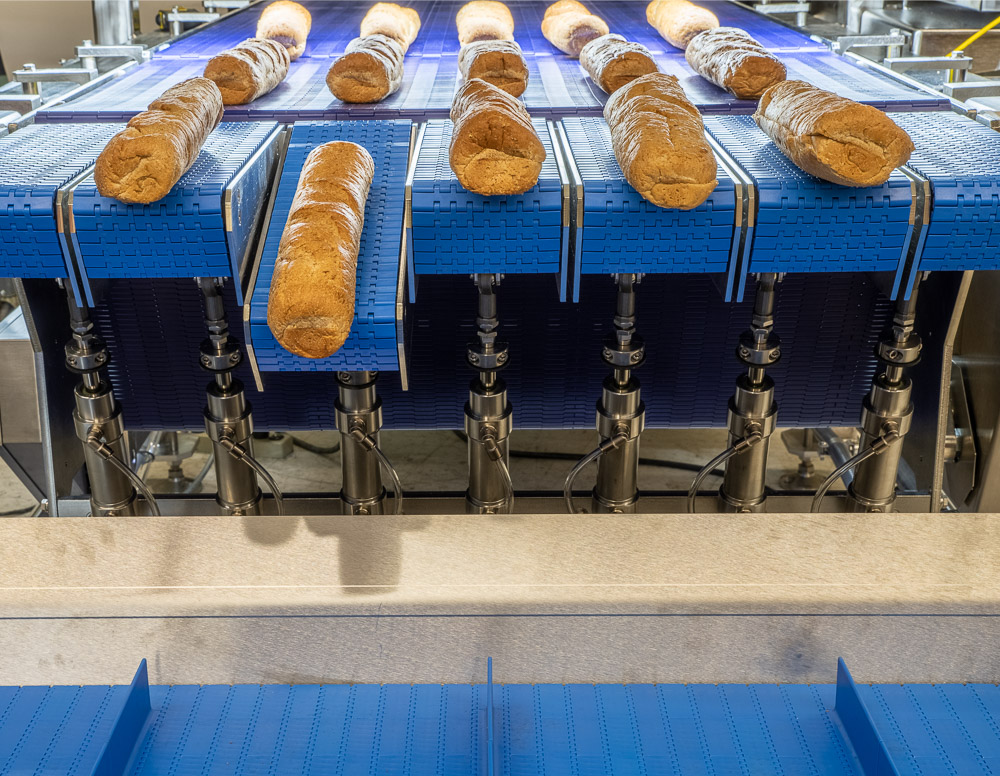
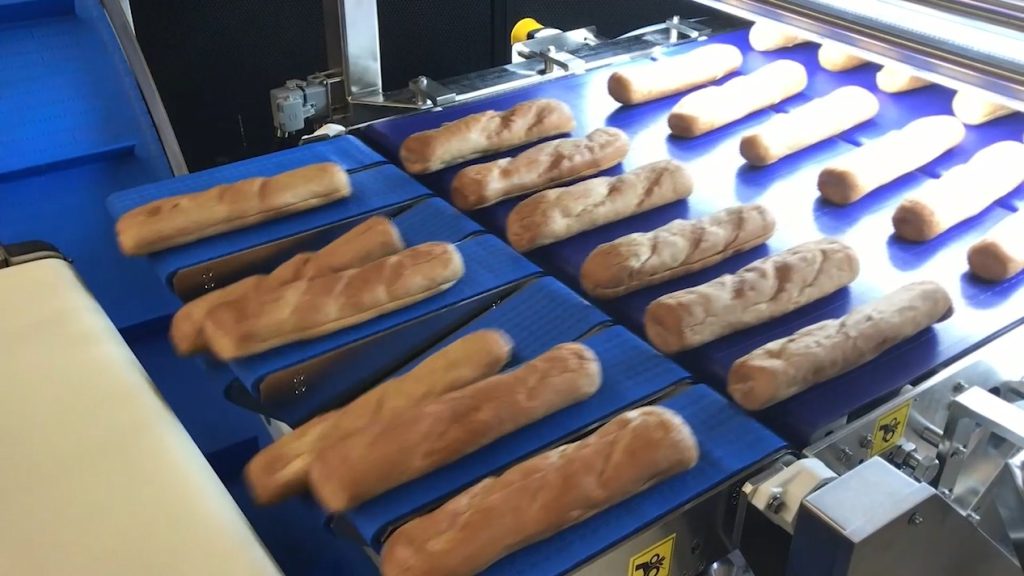
These rejection solutions can be expanded to include a take-away conveyor that feeds into a waste bin alongside the production line. Furthermore, Montrose in-line systems can include a diverter for 100% rejection, diverting all product to the common waste bin.
When used in conjunction with a Montrose in-line or over-line vision inspection system, rejection systems help ensure that out-of-spec products are removed from the production line efficiently at high speeds without disrupting the process. Montrose MTInspect Software collects all measurement grading and rejection data and produces reports in a variety of formats allowing real-time and historical analysis for faults.
Whatever food product that you want to measure, Montrose Technologies has a solution to ensure it is in specification, and those that aren’t are quickly removed.